Imagine your worst nightmare: broken equipment disrupts your activities' smooth progress at the worst possible moment. This makes you lose a lot of time, jeopardizes employee productivity and your company's reputation and could be costly in the end.
Setting an emergency repair plan in place could save the day. If you add a preventive maintenance system, you can avoid this kind of situation altogether! Discover our maintenance, repair and team training services for proper use of your printing and marking equipment.
What does industrial printing maintenance mean?
Equipment reliability is crucial. In order to preserve this reliability, it is important to perform frequent maintenance, which will vary according to your use.
At DMS, we can establish a maintenance plan by working tightly with your production calendar. We can also decide when your machines will need maintenance based on your production. We will plan maintenance at key moments so as not to interrupt production. In other words, during your forecasted production shutdowns. If production never stops, we can temporarily replace your equipment and bring it to our workshop to perform maintenance.
You can sleep with peace of mind, because we take care of everything! Our technical customer service will call in advance to remind you about scheduled maintenance.
The advantages of performing regular maintenance on your marking systems
Regular upkeep of your industrial printers and marking systems offers multiple advantages, such as:
- Extending the life cycle of your equipment
- Reducing shutdown times related to technical issues
- Updating software, which may correct bugs
- Improving the performance of your devices
- Printing that is both clear and long-lasting
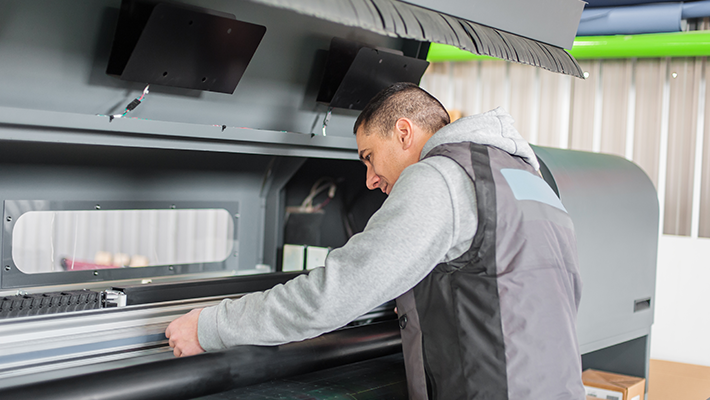
Employee training and awareness concerning industrial printer maintenance
If you do not clean your printers thoroughly or regularly, the printed image message will gradually deteriorate. Printing will be a lower quality and eventually the expiration dates and barcodes could become illegible, which risks affecting the sale of your products. Daily cleaning and good maintenance help avoid these kinds of issues.
In addition, some devices, such as the continuous ink jet Citronix, even have safety settings that display warnings when the machine needs a filter change or printer head cleaning. If several days pass without the maintenance being performed, the printer will automatically shut off and will not restart until the required maintenance is completed. Well-trained employees will be prepared for this scenario.
Good employee training can also make a big difference in identifying a problem that may seem insignificant, in order to solve it immediately instead of waiting for it to become more serious. This kind of mistake could stop or slow your production over the course of several days or even weeks.
We offer virtual and on-site training to teach your employees how to use your marking and printing equipment properly. This training will let your employees be autonomous on a daily basis and learn good practices for using the devices and how to react to possible error messages or malfunctions. We also offer updates or additional training as well as pre-recorded video clips for your new employees.
Our training helps our employees be autonomous in their use of printing and marking systems
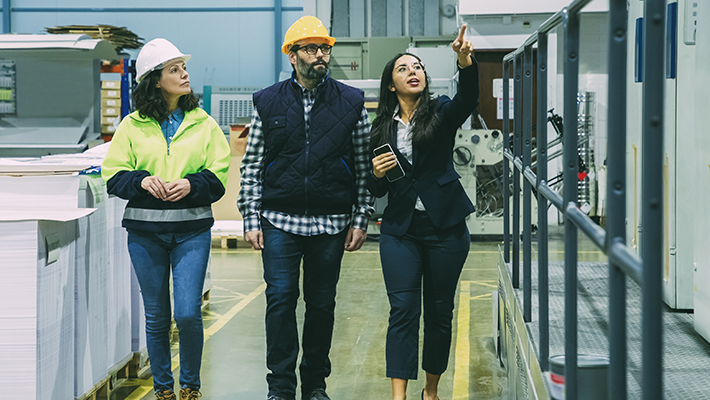
In the event of breakage: our marking system repair services
Did one of your printers suddenly stop working? Did an employee get sick and the replacement doesn't know how to operate the machine? What if your nightmare scenario finally becomes a reality? We can help you with our on-call and year-round emergency repair services.
We can repair your equipment on-site or in our workshop, according to the problem, and during the repair, we can also loan you equipment to avoid costly downtimes. Because we already have most of the parts for the most common brands already in stock, our repairs allow you to get your industrial printers and marking systems back up and running quickly. We also perform on-site tests to make sure everything is functioning properly.
Setting an emergency repair plan in place could save the day
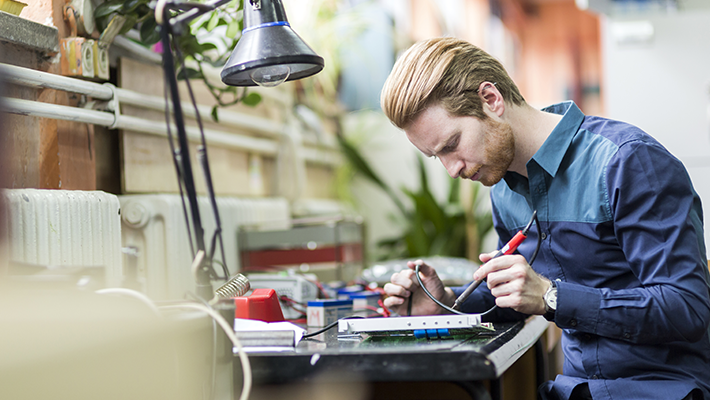
Call on our repair and maintenance services
Take advantage of local repairs that are quick and affordable. Contact us to establish a preventive maintenance and repair plan with one of our advisors or for emergency repairs.